What Is Upset Forging?
Upset forging is one of the most common methods of forging used today and is also known as ‘heading’. It's achieved by placing a pre-heated bar into grooves which hold the bar steadily in position ready for pressure to compress the end of the bar into a die.
Dies, also known as tools, are typically used to widen the diameter of the bar or to increase its thickness. Tools are arguably the most important stage of upset forging as they provide the shape to the forged item. Due to the level of accuracy and intricacy required, they are produced by highly skilled toolmakers, often using state of the art, expensive machinery.
It’s common to have multiple upsetting tools within a set. As a result, the end of the bar is gradually remoulded as opposed to a one-off, radical transformation.
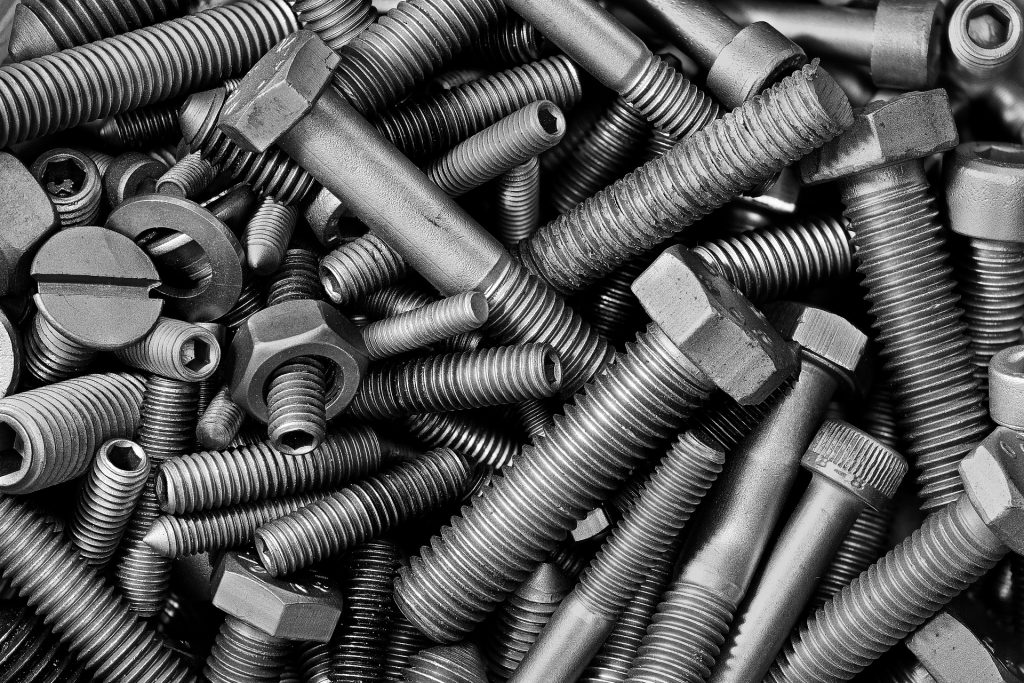
Following the heading stage, the shaped bars may be subject to further hot forged processes to form the material into shapes that are unachievable by using upset forging alone. For example, drop forging is required to punch the hole out of the middle of an eyebolt.
The upset forging process uses a specialised forging press which was initially designed for, and is often still used for, forging the head of a bolt.
Although the upset forging process is fairly flexible due to the use of tools, there are limitation to the change in shape that is achievable by a single blow of an upsetter. The following three rules should be followed to ensure maximum strength in the component:
1. The length of unsupported material should be no more than three times the diameter of the bar. This results in a reduced likelihood of buckling during each upsetting blow
2. If the length of material is greater than three times the diameter, this is still achievable provided that the diameter of the upset is not larger than one and a half times the diameter of the bar.
3. Where neither rule 1 nor 2 can be met, the length of the unsupported material beyond the die must not exceed the diameter of the bar.
Learn more about upset forging in Halesowen and surrounding areas with B.B. Price, and contact us for your next project.
Our Upset Forging Facilities
Upset forging is one of a number of forging processes we offer from our Rumbow Works site in Halesowen, West Midlands.
At B.B. Price we have our own in-house toolroom. This is equipped with state-of-the-art CNC and spark erosion machines and is staffed by highly skilled and experienced toolmakers. Accordingly, we aren't dependent upon third parties to provide us with tools/dies that are required to produce bespoke patterns.
Firstly, offering this service means we have greater control over our entire production cycle. As a result, we are able to provide greater assurance over our product quality. Additionally, we are able to prioritise our workflow to minimise lead times on customers' urgent requirements.
Our upset forging capabilities span from steel sections with diameters of 10mm up to 50mm.
Examples of our product range that are manufactured using upset forging include:
Ready to find out more?
Contact our experts regarding your forging needs.